Как делают бутсы: Как делают бутсы Nike — Football Style — Блоги
Как делают бутсы Nike — Football Style — Блоги
Блог Football Style побывал в Италии и собственными глазами увидел, как 15 человек на небольшой фабрике Nike в городке Монтебеллуна на севере Италии делают бутсы для лучших футболистов мира.
Фабрика в Монтебеллуне была основана в 1996 году и первоначально штат сотрудников состоял лишь из трех человек — двух инженеров и менеджера по работе с атлетами. За 16 лет число работников увеличилось в несколько раз, достигнув 15. Именно они и делают бутсы для Иньесты, Криштиану Роналду и других суперзвездных парней (к слову, слепок стопы Марии Шараповой также был там обнаружен).
Гостей встречают бутсы Роналдиньо:
Фотографии японского полузащитника «Интера» Нагатомо Юто и швейцарца Валона Бехрами.
Директор фабрики Кендалл Шапиро оказался крайне веселым мужчиной и рассказал об основных аспектах работы Nike, заключающихся в использовании инноваций и стремлении к прогрессу.
Маттео Тессаро, один из первых работников фабрики, а ныне главный инженер, на стенде показал основные части всех четырех главных бутс в линейке Nike к чемпионату Европы.
Вообще, новая коллекция Nike выглядит следующим образом. Первым номером слева направо стоят синие CTR360 Maestri II, символизирующие надежную и уверенную игру полузащитников; вторым — классические Tiempo Legend, созданные для плеймейкеров — в них легко и удобно обрабатывать мяч и отдавать точные передачи; далее — Laser IV, предназначенные для максимально точных ударов и, наконец, Mercurial Vapor VIII — самые скоростные бутсы, состоящие из минимального количества деталей.
В Mercurial Vapor VIII, по ощущениям, играет чуть ли не вся атакующая сила российской премьер-лиги. Сходу без всяких подсказок вспомню Аршавина, Широкова, Смолова, Дзюбу и Джуджака (товарищи Роналду и Ибрагимович также пылят в них). Мне показалось, что модель для Евро не настолько яркая и запоминающаяся из-за присутствия белого.
На первом этапе производится сборка верхней части бутсы — составные элементы сшивают при помощи промышленных швейных машин. На самом деле, меньше всего таких частей у Mercurial Vapor VIII.
Весь процесс производства — от необходимой температуры до положения элементов на приборах зафиксирован в специальной книге. Вообще, это требуется для контроля качества продукции из-за требований стандартов серии ISO.
Подошва Mercurial Vapor VIII очень гибкая, но прочная:
После того, как верхняя часть готова и шнурки вправлены, ее надевают на слепок ноги атлета:
Вот так выглядит макет стопы Криштиану Роналду:
При помощи специального аппарата к основе пришивают стельку и фиксируют ее:
После этого прикрепляют подошву:
Которую предварительно необходимо покрасить:
После этого бутсы отправляют под специальный пресс, ну а потом чистят и устраняют все визуальные недостатки.
Потом бутсу можно снять со слепка:
Проверить ее готовность:
И переходить к последней стадии — нанесению визуального оформления. Кто-то просит нанести на бутсы собственную фамилию, кто-то — государственный флаг, кто-то — имена близких, ну или аккаунт в твиттере.
Вильфред Боума теперь совершенно спокойно может отправляться на Евро — его обувь готова.
У каждого атлета, сотрудничающего с Nike, есть собственный профайл, в котором указана вся необходимая информация. Поначалу каждому футболисту привозят по две пары бутс, в которых он тренируется и вносит какие-то поправки. Если же все хорошо, то к нему прилетают еще две.
Пометки в профайле Аршавина говорят о необходимости нанести российский флаг и фамилию с 10 номером.
Третий пункт с пометкой Фергюсон в скобках (тот самый Барри из «Рейнджерс») говорит о необходимости оставить задник мягким, без подкладки, что объясняется анатомическим строением стопы футболиста. На фото это свойство демонстрируется на примере бутсы Романа Широкова, в профайле которого указано то же самое.
Стопка коробок с бутсами россиян оказалась чуть ниже только лишь испанской:
Кстати говоря, бутсы Василия Березуцкого для Евро в любом случае достались бы и Алексею, — братья заказывают их на имя первого.
Коллеги из других стран. Крайний слева очень похож на молодого Иосифа Пригожина if you know what i mean.
Мужчина из греческого contra.gr (можно сходить на сайт и посмотреть, как выглядит самый популярный спортивный сайт страны) все время оказывался рядом с эпицентром действия и заснял небольшое видео того, как очищают бутсы.
А это Арья Йога из Nike. Он как-то сфотографировался в форме пражской «Спарты» и стал всем говорить, что он футболист.
Тут по сей день любят Роналдиньо и Роналдо:
И помнят Обафеми Мартинса:
Кендалл, Мауро, Маттео, две симпатичные девушки и еще 10 человек своими руками делают бутсы для лучших футболистов мира.
Cleats — как производятся футбольные бутсы — Около футбола — Блоги
Всем привет!
Тема сегодняшнего материала немного необычна. Пожалуй, она не будет интересна массам, но своего читателя, я уверен, найдет. Все фото, как всегда, кликабельны.
Итак. После недавних печальных событий в Манчестере, я случайно наткнулся на твиттер Криштиану Роналду с соболезнованиями (по-человески выражаю сочуствие всем, кто пострадал в этом чудовищном происшествии). Клик за кликом, и я уже прокручивал «ленту» португальца. Фотографии с празднования чемпионства, фото с сыном, фото с фотосессии, реклама Nike, фото из раздевалки… Стоп. Nike. Далее ход моих мыслей объяснить трудно. Пожалуй, это было, что-то типа Ronaldo – реклама Nike – бутсы CR7 – бутсы Nike – как делают бутсы.
«Аватарка» Роналду в твиттере.
О последнем элементе в этой «логической» цепочке я сегодня и расскажу.
Большая часть материала не будет отсылать вас к определенному производителю, но конкретные примеры мы рассмотрим именно на Nike.
Сразу оговоримся, что история «бедные африканские рабочие производят кроссовки в рабских условиях фактически за еду. Причем левый кроссовок делается в Уганде, а правый в Зимбабве» — к крупным и, действительно, качественным производителям не относится (спойлер — их делают в Китае).
И последний, общий нюанс: речь пойдет только о бутсах, предназначенных для профессиональных футболистов, играющих на натуральном газоне.
Что, по идее, представляют из себя самые обычные футбольные бутсы, какова их главная задача? В общем смысле – это ботинки с шипами, которые впиваясь в траву должны всегда придавать вертикальное положение игроку (при старте, рывке, беге, прыжке).
Сейчас, в век современных технологий, у производителя есть возможность проводить компьютерный анализ, вставлять различные датчики в свою продукцию, дабы понять, какие конкретно механические свойства нужны игрокам (не забываем, что бутсами пользуются не только футболисты), чтобы показывать свои лучшие качества.
Некоторые гиганты обувной индустрии даже адаптируют свой товар для конкретно позиции игрока на поле.
По заявлениям руководства Nike, сейчас они специализируются на двух линиях футбольных бутс.
Первая для много бегающих игроков – тех, кто совершают резки рывки вперед или вынужденных быстро возвращаться назад (линейка Mercurial). Вторая для больших парней, которые как правило отрабатывают в защите и должны твердо стоять на ногах в любой момент (линейка Vapor).
Сами бутсы изготавливаются из различных материалов, опять же в зависимости от цели и позиции на поле. Например, термо-нейлон достаточен жесток, но слишком легок для резкого или неожиданного толчка.
При изготовлении бутс Nike использует цифровой «анализ конечных элементов». Это позволяет дизайнерам «играть» с расположением шипов, их длиной и диаметром. Распечатанные на 3-D принтере образцы, фактически тут же позволяют провести «тест в живую». Далее, проверяется давление от ноги на каждый шип. Если что-то не устраивает, то изменяется геометрия шипа и все проверяется вновь.
По словам вице-президента компании, Макса Блау, такая методика работы значительно ускоряет процесс изготовления.
Также современные технологии уже привнесли кое-что новое в сами бутсы. Например, анализ, название которого приведено абзацем выше, позволил создать «лопастной» шип, который дает возможность игроку стартовать более резко. Шип конусообразной формы помогает футболистам менять направление движение с меньшей потерей скорости, в то время как шипы с другой геометрией способствуют замедлению игрока (в зависимости от наклона поверхности).
Типичная пластина футбольной бутсы, как правило сочетает в себе конусно и V-образную форму. Давление в шипах выравнивается через пластину.
Пожалуй, главной задачей производителей бутс является уменьшение размеров (особенно диаметра) шипов. Чем меньше диаметр, тем меньше проникновению в поверхность, а это означает меньшее усилие для подъема ноги.
Кстати, интересный момент, другой гигант спортивной формы – Adidas – использует L-образную шпильку для игроков в американский футбол. Такая конструкция позволяет заметно уменьшить скольжение, а игроки могут выполнить быстрый разворот и остаться в устойчивом положении.
Коли заговорили о немецком концерне, стоит упомянуть, что они разрабатывают 4 линейки бутс для игроков в американский футбол и 3 для обычного футбола.
Пожалуй, главным различием в бутсах для американского и обычного футбола, являются конструкции регулирующие поперечную тягу. В футболе движения больше угловые. К тому же игроки в американском футболе довольно крупного размера и это приводит к увеличению количества шипов.
Ах да, еще на бутсах для игры в соккер есть шипы в области пятки.
Упомяну еще и бейсбол. Здесь в бутсах преобладают металлические шипы. Это более удобно в случае бега по грязи.
С основными принципами разобрались, переходим к материалам.
Сейчас, наиболее популярное «сырье» — углеродное волокно. Оно не только очень прочное, но и легкое. Те же Nike Super Light весят около 190 грамм. А самые-самые легкие бутсы того же Nike – 160 грамм.
Углеродное волокно прошивается под углом, что также придает прочность.
Еще одной интересной особенностью является пластина. Она состоит из семи слоев карбонного материала в сочетании с полиуретаном и ТПУ (термопластичный полиуретан). Специальные ребра жесткости придают стопе необходимую фиксацию и защищают от самых жестких ударов.
Также в качестве «сырья» используют природные и переработанные материалы. Пластина на био-основе, как правило, создается на кастровых (фасолевых) бобах. Это придает ей необходимую гибкость. Вкладыш носка также создается из бобовых. А шнурки, подкладки, «язык» — на 70% состоят из переработанных материалов.
Задник может укрепляться маслом из фасолевых бобов.
Основные пункты, о которых я хотел рассказать, мы рассмотрели. Остался еще один очень важный вопрос – где все это производится?
В самом начале текста, я немножко покривил душой. Дело в том, что тот же Nike фактически не владеет фабриками по производству обуви. Как правило, компания просто нанимает какой-нибудь обувной завод, поручая ему заказ. Обувь Nike никогда не производится в США, самые крупные заводы (нанимаемые) находятся в Китае, Индии, Вьетнаме. Сам «производитель» предпочитает концентрировать на дизайне, технологиях и маркетинге. Хотя, мне трудно представить, чтобы бутсы для Роналду шил некий Ли Хуань из деревни Ю-Ху (имена персонажей вымышленные, все совпадения носят случайный характер).
Настало время статистики и конкретных примеров. В процессе подготовки материала я наткнулся на такой вот сайт — Football Boots (думал я один такой шизанутый на околофутбольной теме, оказываются есть люди и похлеще)
Давайте по порядку. Бутсы какой фирмы пользуются наибольшим спросом среди футболистов.
1) Nike – 54.8%;
2) Adidas – 36%;
3) Puma – 5.7%.
Самой популярной линейкой является Mercurial.
А вот какие бутсы носят самые известные футболисты.
Кстати, на этом же сайте можно составить свою символическую сборную и посмотреть кто, что носит. Так как я являюсь фанатом «Юнайтед» то собрал сборную «красных дьяволов» и заодно свою символическую сборную мира.
Символическая сборная бутс «Манчестер Юнайтед»
Символическая сборная бутс мира
Давайте вкратце рассмотрим бутсы игроков (по одному из каждой позиции).
Да не обидится на меня Месси, но из нападающих я возьму Криштиану.
Nike Mercurial Superfly V
Если верить обзору сайту my-soccer, данные бутсы обладают безупречной анатомической посадкой. Для этого используются технологии Flyknit (конструкции верха), Dyanmic Fit (носок) и Flywire (нити). По заверениям разработчика, нога фиксируется настолько хорошо, что её движения создают ощущения, что бутс фактически нет.
Большое внимание уделено контакту ноги с мячом. Технология NikeSkine гарантирует цепкость материала с мячом, позволяя контролировать его на любой скорость.
Также, Nike уверяет, что комбинация шипов гарантирует отличное сцепление (с газоном) при любом качестве поля и погоды.
Самый лучший игрок АПЛ этого года —Нголо Канте — пользуется бутсами Adidas X16+ Purechaos (весьма символической название – чистый хаос)
Главной особенностью таких бутс является отсутствие шнуровки, а технология techfit позволяет обуви не растягиваться.
Специальная подкладка в области пятки обеспечивает комфорт даже при резкой смене движения.
Один из лучших защитников мира (на мой взгляд) Леонардо Бонуччи пользуется бутсами Nike Magista Obra II.
Вот что по поводу этих бутс говорит «создатель»:
Технология Dynamic Fit в области голеностопа создает более прочную структуру между стопой и голенью, не сковывая движений
Рельефный верх для лучшего контроля мяча
Трикотаж в области голеностопа и под шнурками для зональной амортизации
Эластичный верх Flyknit без язычка для поддержки и вентиляции
Технология Nike All Conditions Control (ACC) для оптимального контроля мяча как в сухую, так и во влажную погоду
Внутренний задник для надежной посадки.
А вот голкипер «Манчестер Юнайтед», Давид де Хеа, предпочитает бутсы Adidas. Испанец носит X16.1 Leather.
Конструкция этих бутс максимально легкая и практичная дает возможность игроку первым оказаться в месте для атаки.
Верх обуви цельный techfit® без единого шва обеспечивает отличное облегание стопы, тем самым освобождая игрока от траты времени понапрасну на разнашивание и шнуровку.
Облегченная подошва Sprintframe позволяет игроку чувствовать себя комфортно даже на высокой скорости ведения мяча.
Итак, подведем краткие итоги сегодняшнего материала:
1) Бутсы теперь можно печатать и на 3-Д принтере;
2) Главная направление в развитии бутс – уменьшение веса и размеров шипов;
3) В качество основного материала используется углеродное волокно и натуральное сырье;
4) Конструкция бутс может отличаться в зависимости от позиции игрока;
5) Конструкция бутс зависит от вида спорта;
6) Гиганты индустрии больше занимаются дизайном и технологиями, а производят бутсы на наемных заводах;
Бонус:
Видео 2009 года как делаются бутсы
Как изготавливаются кожаные сапоги — компания Friday Boot Company
От планирования до постпродакшна мы проходим этапы изготовления наших ботинок.
Каждый предмет обуви Четверга изготавливается вручную в течение нескольких недель в ходе трудного, но полезного процесса. В то время как многие обувные компании срезают углы, Четверг вкладывает время и усилия в производство обуви, которая прослужит всю жизнь при надлежащем уходе. Для создания лучших продуктов у нас работают высококвалифицированные мастера с многолетним опытом. Как недавно объяснил владелец одной из крупнейших в отрасли независимых обувных фабрик, «Thursday очень серьезно подходит к качеству. Они уделяют очень пристальное внимание деталям. Они не читают отчет о качестве и не откладывают его в сторону, они разбирают его на части». В то время как наши конкуренты часто используют кожу более низкого качества, более дешевую фурнитуру и пропускают проверки качества, успех нашего конечного продукта в буквальном смысле зависит от нас.
1
Дизайн
Мы начинаем с того, что спрашиваем наших клиентов, чего они хотят. Мы собираем отзывы с помощью опросов, личных бесед, взаимодействия в социальных сетях и по ряду других каналов. Эти данные передаются нашим дизайнерам, которые используют их для создания неподвластных времени стилей, столь любимых сегодня, какими они будут через 50 лет.
Проекты проходят проверку. Многие дизайны не проходят первое рассмотрение, а те, что выдерживают, рассматриваются месяцами.
После того, как дизайн обуви завершен и утвержден, мы отправляем нашим фабрикам «технологический пакет», который включает в себя все характеристики обуви, вплоть до размера отверстий для шнурков, которые они используют в качестве карты для физического продукта.
2
Plan & Source
Мы работаем с нашими фабриками, чтобы определить точные потребности в материалах для производства. После расчета количества мы заказываем кожу, подошвы, фурнитуру и шнурки у наших поставщиков в США, Мексике и Италия.
3
Производство
Когда материалы от наших субпоставщиков поступают на завод, мы проверяем их, распаковываем и подготавливаем к производственному процессу.
Разворачиваем кожу, отрезаем кусок размером с занавеску для душа, растягиваем и расправляем.
Затем мы прослеживаем рисунок ботинка, избегая любых дефектов, таких как шрамы, царапины и морщины — любые части кожи, которые вам не нужны на обуви.
Мы нарезаем детали и зачищаем (сглаживаем) края, чтобы они не были слишком толстыми, когда они накладываются друг на друга в процессе сшивания.
После раскроя берем кожаные детали верха будущего ботинка и сшиваем их между собой.
Этот большой кусок сшитой вместе кожи имеет мягкую кожаную подкладку с помощью клея и швов.
Очень аккуратно, люверсы пробиты вручную.
Плоская шкура теперь приобретает новое измерение благодаря сшиванию в форме, примерно напоминающей ботинок без подошвы.
Затем из большого куска кожи формируется колодка, представляющая собой кусок пластика или дерева, напоминающий по форме ступню.
Используя прочную машину, кожаный верх равномерно натягивается на колодку, а лишняя кожа, свисающая с низа, обрезается.
Нижняя часть верха, еще на колодке, снабжена прорезной полосой вдоль нижней стороны. Эта полоска представляет собой длинный и тонкий кусок кожи, который в конечном итоге соединит верх с подошвой.
Ребристый слой добавляется, чтобы дать ботинку границу для поддерживающего слоя.
В пределах ребра фанеры забит стальной стержень и зацементирован жидкой пробкой.
После частичного высыхания пробки ее разглаживают, чтобы обеспечить равномерное распределение.
Промежуточная подошва — это следующий слой, который представляет собой комфортную полосу DuraEVA, часто используемую в спортивной обуви из-за ее способности поглощать удары, или кусок толстой кожи, в зависимости от модели.
Затем приклеиваем подошву. Независимо от того, сделана ли она из кожи, резины или того и другого, подошва является самым внешним слоем подошвы.
Вся подошва усилена по отношению к верхней части с помощью ранта Goodyear, что означает, что стежки прошиваются через каждый слой подошвы до полосы ранта.
С помощью шлифовального станка подошва обрезается до однородной формы.
Затем в ботинок вставляется стелька.
На наружную поверхность верха наносится финишный крем.
Шнурки наложены.
Сапог проверен на качество.
4
Упаковка
Малоизвестный факт, что наша обувь упаковывается на заводе, а не на складе. Наши ботинки упаковываются в полиэтиленовые пакеты, кладутся в коробку с надписью «спасибо» и проходят окончательную проверку.
Ботинки в коробках отправляются на склад.
Дизайн
Как изготавливаются ковбойские сапоги
Есть много-много шагов, чтобы сделать сапоги в стиле вестерн, сделанные на заказ. Некоторые вы можете увидеть, когда держите ботинок в руке, другие скрыты от глаз, когда ботинок закончен и готов к носке. Ниже приводится краткое описание шагов, необходимых для изготовления загрузки… щелкните любую из фотографий, чтобы увидеть ее крупным планом.
(Ботинки, показанные на этой странице, мы, Дженнифер Джун, сделали в магазине обуви Текса Робина в Коулмане, штат Техас, с 10 июля по 3 августа 2000 года. )
Я хотел бы поблагодарить мистера Текса Робина за его редакторский вклад в эту статью… и, что более важно, я хотел бы поблагодарить Текса за то, что он помог мне осуществить мою мечту стать сапожником благодаря его щедрым предложениям времени, опыта и личной поддержки.
Как сделать сапоги в стиле вестерн Деннис Коттл и Дэйв МакКинни. Для заказа свяжитесь с г-ном МакКинни по телефону (817) 688-2289..
Техасская загрузочная книжка Дэвида Рейффа. Penguin Books, 1980. (Доступно на сайте abebooks.com.)

ботинка, который крепится
пришиваем к союзке.

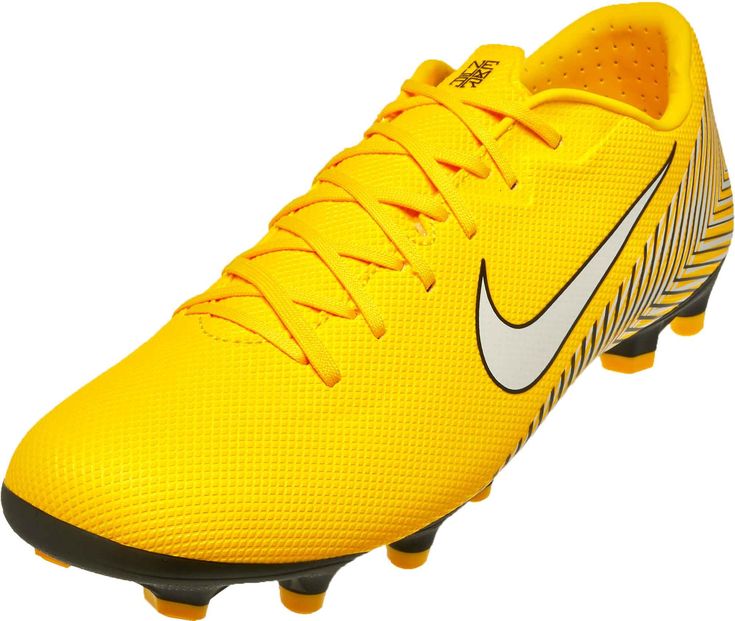
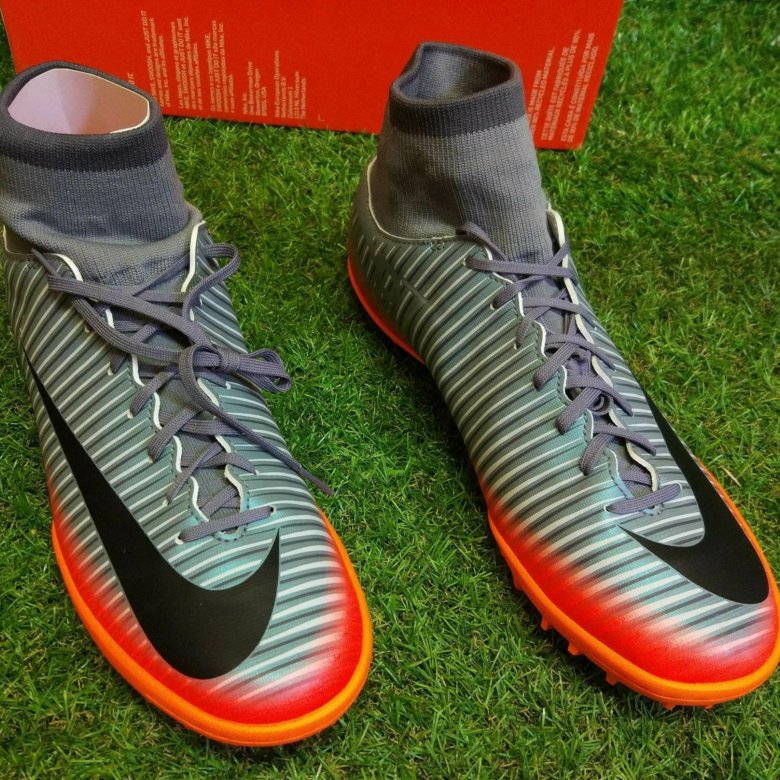
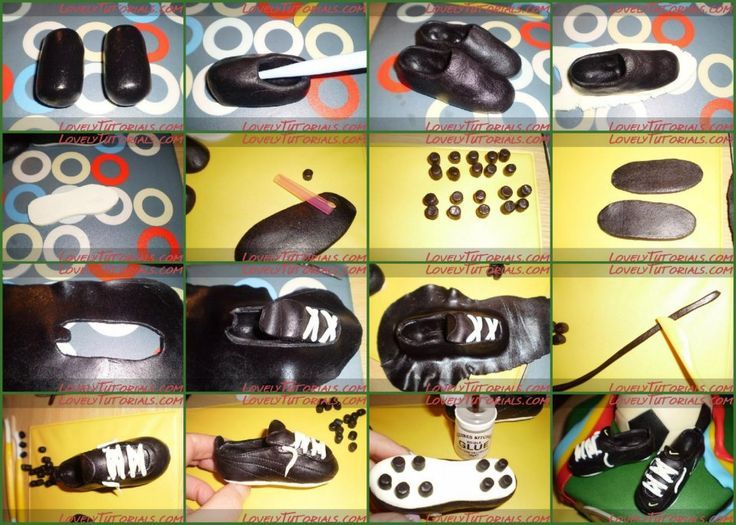
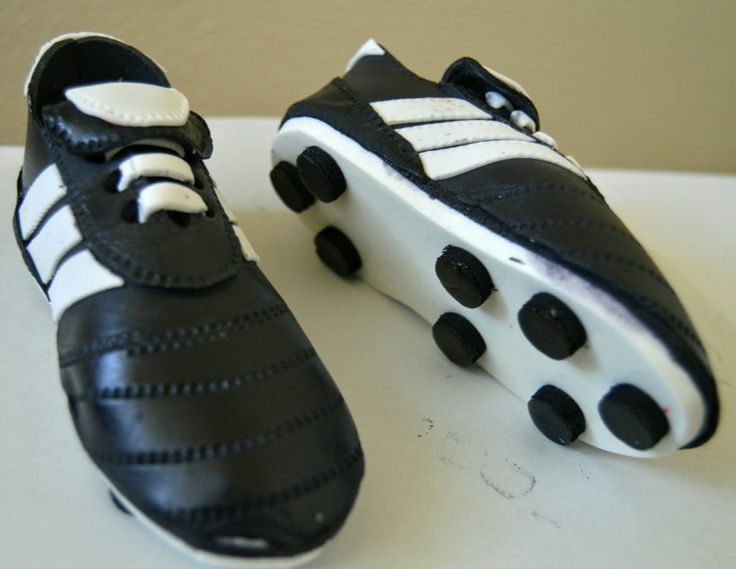